
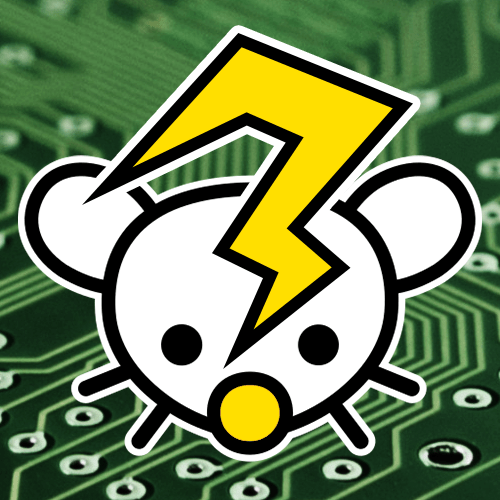
If you can wait a couple weeks, AliExpress is going to be the cheapest.
eBay may be a bit more expensive, but it’s often my go-to because you can find everything and usually there are options with short shipping times.
For not too obscure parts, I would look at Reichelt, their prices are surprisingly low (especially if you bundle your orders to save on shipping costs).
Every single freewheel does this, and it’s not an issue.
The freewheel bearings don’t line up exactly with the wheel bearings. This is always the case to some degree, because the interface between freewheel and hub is a non-precision thread.
It might look weird when freewheeling, but once you put use the pedals, freewheel and hub are rotating together, negating this wobble.